Semester 2 - Blog Post #1
- Team 22
- Feb 5, 2021
- 2 min read
Over the winter break, our team has made progress toward gathering specialty components. The belt and complimentary sprockets have already arrived and are ready for assembly. The water wheels and gears that were designed by the team have already been sent to the 3D printing lab.
During this period, the one challenge that we have encountered was with the 3D components. We had been given the wrong printer size restrictions last semester, so we had to downsize the parts to fit in the machine. The gears were originally 9 and 5 inches in diameter, but needed to fit in the printer’s 8 inch cube. We decided to bring the attached axles closer together to decrease the size of the gears to 7.5 and 6.5 inches.
For the water wheels, it was a bit more difficult. The belt’s movement depends on the torque supplied by the wheels, so the outputs from the wheels had to stay the same while the dimensions changed. To achieve this, we increased the length of the blades so that the water could work on a greater surface area. The decreased force distance was balanced with increased force which allowed us to keep the same torque.
The above pictures are the water wheel and gears CAD drawings with the new dimensions. They have been sent to the 3D printing lab to be approved and printed.
As the custom unique parts have arrived, our team will now be procuring standard items from Home Depot and Amazon as we wait for our 3D printed parts to be constructed by the 3D printing lab. If the printed parts arrive early enough, we will also begin the fabrication of the first prototype. Although we planned to start construction before, the changes in our design delayed our construction. However, we still plan to finish construction on our first prototype as scheduled to give us room for any changes that may need to be made.
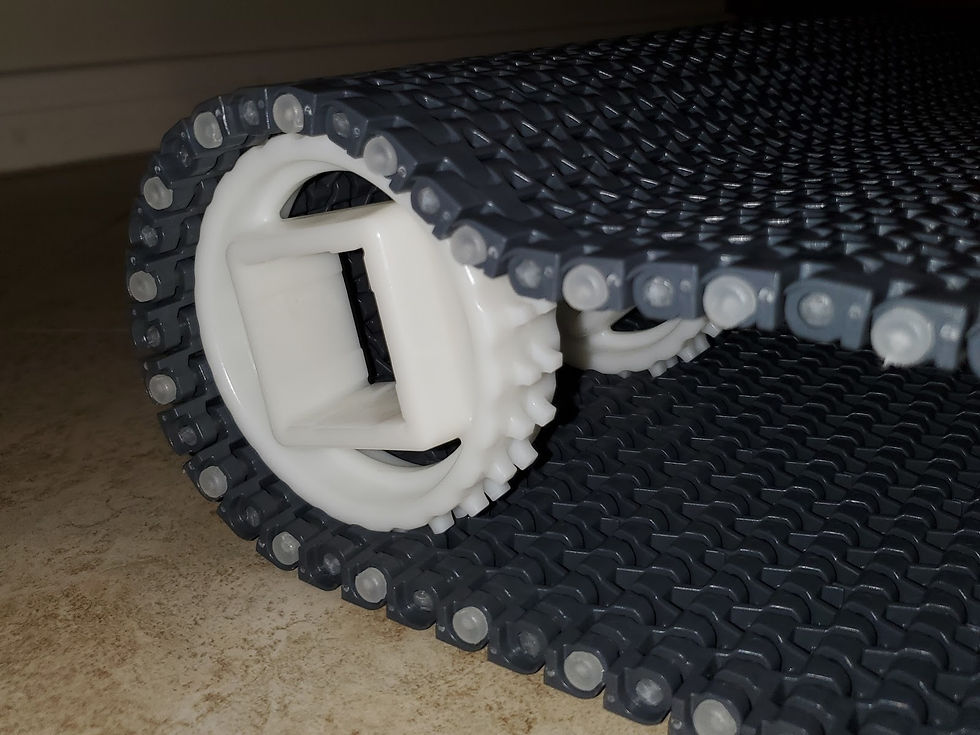
The belt and sprockets have arrived and are ready for assembly.
Fortunately, all the parts necessary for our first prototype are available however, a challenge we may face is finding the right sized square shafts for the sprockets. Furthermore, we need to find square-circle conversion connectors because the bearings in the same axle will need circular connections. Another challenge we may face is time of retrieving the 3D printed parts from the lab. We would like to begin construction as soon as possible to confirm every part functions as designed. If there are any unforeseen circumstances, we would use the extra time to make the appropriate changes to ensure successful performance.
Comments